Sustitución del sistema de Freno/Clutch neumático en máquina niveladora.
El mantenimiento adecuado de una máquina niveladora es fundamental para garantizar su rendimiento óptimo y prolongar su vida útil. Entre los componentes más críticos que requieren atención periódica se encuentran el sistema de frenos y el embrague (clutch), ya que son esenciales para la seguridad y eficiencia operativa del equipo.
En la industria del acero, la precisión y la calidad son factores determinantes para garantizar que los productos finales cumplan con los estándares exigidos por el mercado. Una de las herramientas clave en este proceso es la máquina niveladora, un equipo especializado diseñado para corregir irregularidades y deformaciones en las planchas o bobinas de acero, asegurando que estas adquieran una superficie plana y uniforme.
En una empresa de aceros, la máquina niveladora no solo es sinónimo de calidad, sino también de eficiencia. Al garantizar que las planchas o bobinas de acero cumplan con las especificaciones dimensionales requeridas, se reduce el desperdicio de material y se optimizan los procesos posteriores, como el corte, el doblado o el estampado. Además, contribuye a mejorar la productividad, ya que un material bien nivelado facilita su manipulación y procesamiento en las siguientes etapas de producción.


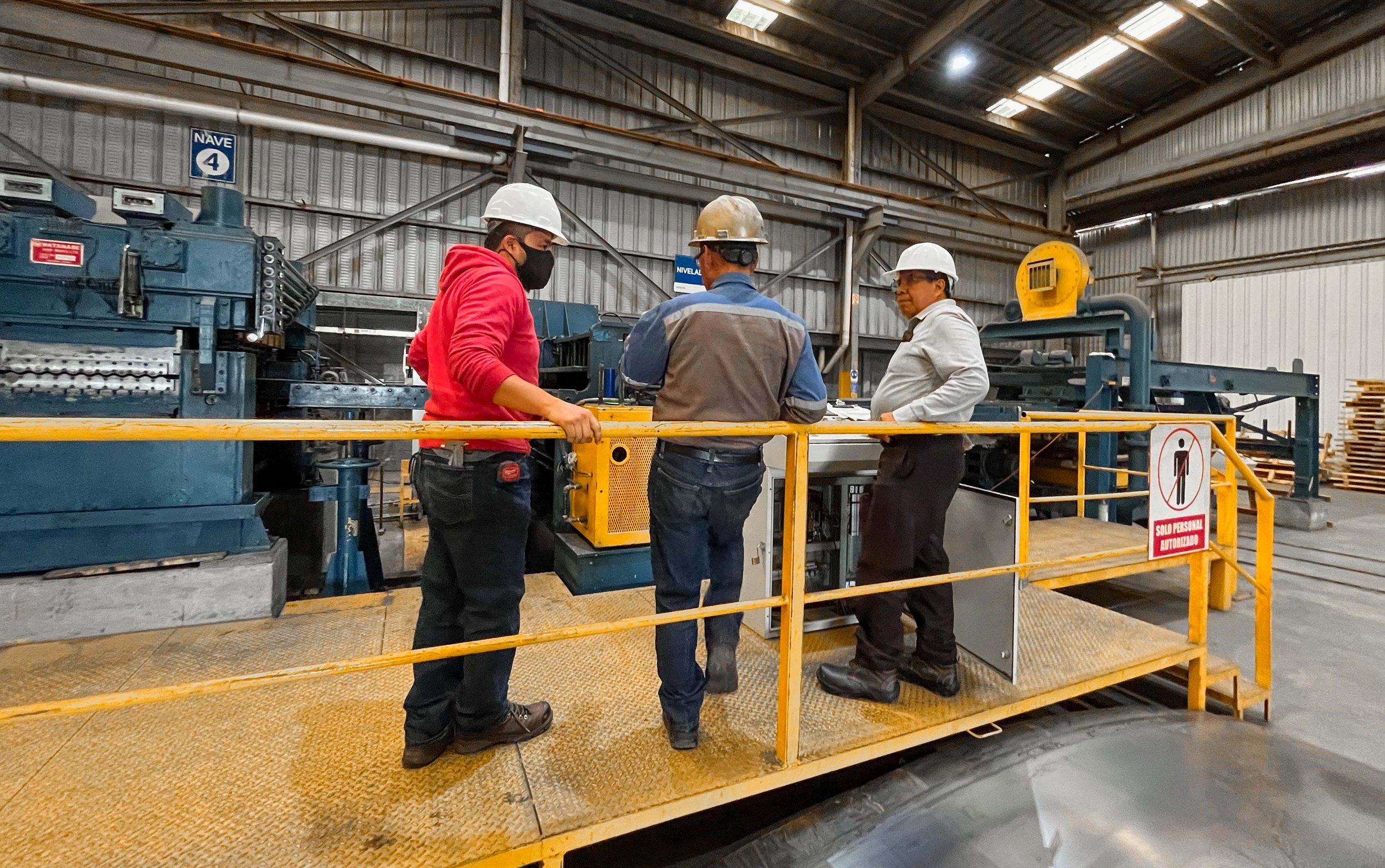
Cuando realizamos la primer visita a la máquina niveladora, detectamos que presentaba fallas significativas en el sistema de corte, el cual funcionaba mediante un mecanismo de freno/clutch neumático. Este sistema presentaba numerosas deficiencias, lo que provocaba paros constantes y afectaba la eficiencia operativa.
Nuestro principal desafío era implementar una solución que permitiera optimizar y mejorar el rendimiento del sistema de corte, garantizando su funcionamiento continuo y confiable.



La primera tarea consistió en desmontar el antiguo sistema de freno/clutch neumático, el cual presentaba un desgaste considerable y ya no cumplía con los estándares de operación requeridos.
Durante este proceso, fue fundamental tomar mediciones precisas y documentar las especificaciones técnicas del sistema existente, con el fin de garantizar que las nuevas adaptaciones mecánicas se integraran de manera óptima y cumplieran con las exigencias de rendimiento y funcionalidad del equipo.
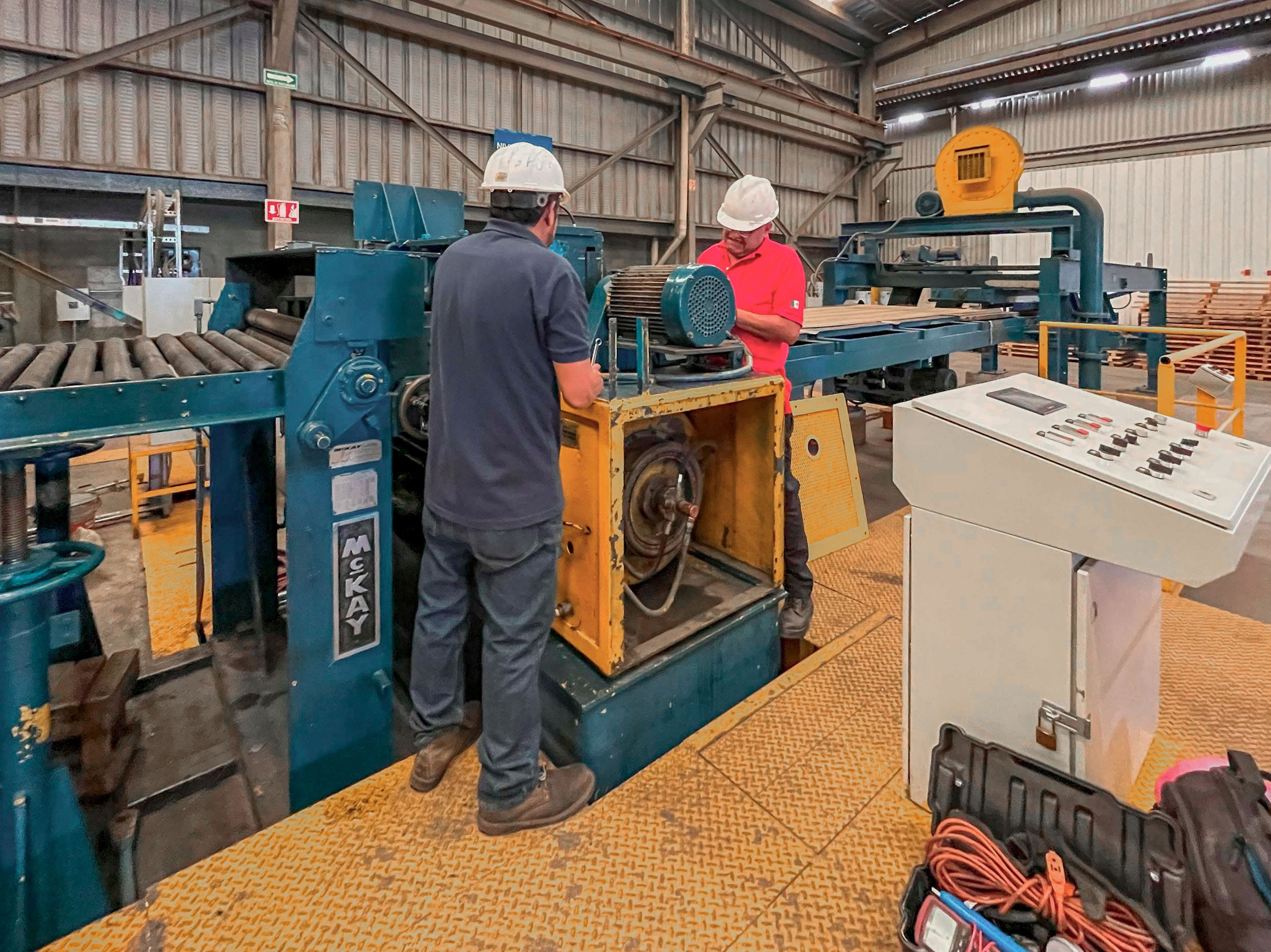


En el proceso de modernización y mejora del sistema de corte de la máquina niveladora, se llevó a cabo la integración de un gabinete de control especializado, diseñado para gestionar y optimizar las operaciones de corte con precisión y eficiencia. Este gabinete funciona en estrecha coordinación con el primer gabinete, que es el encargado de la operación general de la máquina, creando un sistema interconectado y altamente automatizado.
El nuevo gabinete de control de corte incorpora tecnología avanzada de la marca Mitsubishi, garantizando confiabilidad y rendimiento de clase mundial.



En el ámbito mecánico del proyecto, se llevó a cabo la instalación de un servo de primera generación marca Mitsubishi, un componente de alta precisión y confiabilidad diseñado para operar en condiciones exigentes. Para garantizar su correcto funcionamiento y adaptación al sistema existente, fue necesario realizar una serie de modificaciones y adaptaciones mecánicas, las cuales fueron cuidadosamente planificadas y ejecutadas.
Se desarrolló una base robusta y resistente, específicamente diseñada para soportar el peso y las vibraciones generadas durante la operación de la máquina. Esta base asegura la estabilidad del servo, evitando desalineaciones y garantizando un rendimiento óptimo.
Se fabricaron catarinas y componentes mecánicos adicionales, maquinados con tolerancias precisas para garantizar un acople perfecto con el sistema existente. Estas piezas fueron diseñadas para resistir el enorme desgaste generado por las operaciones continuas y las cargas mecánicas a las que estarían sometidas.



Todas las nuevas piezas y adaptaciones fueron concebidas con un enfoque en la durabilidad y resistencia, teniendo en cuenta las condiciones extremas de trabajo a las que estarían expuestas. Se seleccionaron materiales de alta calidad y se aplicaron tratamientos superficiales para aumentar su vida útil y reducir el mantenimiento requerido.


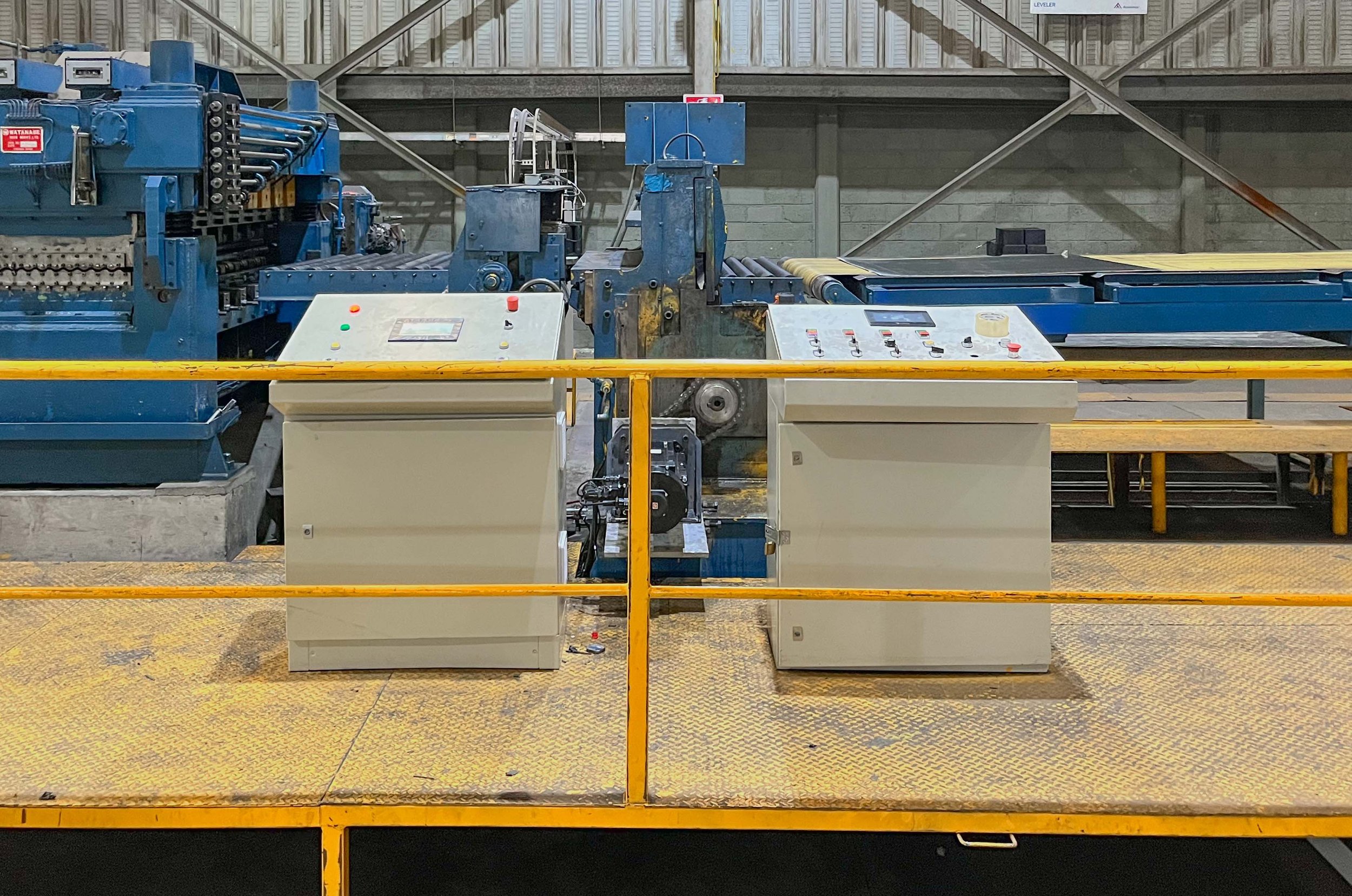
Como último paso, se realizó una revisión exhaustiva de los detalles de programación para proceder con las pruebas de funcionamiento. Estas pruebas se llevaron a cabo utilizando lámina de calibre 14, un material que anteriormente presentaba problemas significativos durante el proceso de corte, como alto desperdicio y paros constantes que afectaban la eficiencia operativa.
Tras las pruebas, se confirmó que el nuevo sistema operaba con precisión y sin interrupciones, resolviendo los inconvenientes previos y optimizando el proceso.
Finalmente, se entregaron los diagramas eléctricos y mecánicos actualizados, junto con los manuales de operación detallados, que incluyen instrucciones claras para el uso y mantenimiento del sistema. Además, se capacitó al personal técnico y operativo, asegurando que contaran con el conocimiento necesario para manejar el equipo de manera eficiente y segura.
Este proceso integral garantiza que la máquina niveladora esté lista para operar a su máximo potencial, reduciendo tiempos de inactividad y mejorando la productividad.
Te dejamos todo el proceso completo en un video.
Este proyecto es un claro ejemplo de cómo la modernización de equipos antiguos puede traer beneficios notables en términos de eficiencia y confiabilidad. Estamos orgullosos de nuestro equipo de AQUA PROJECTS, por su dedicación y habilidad para llevar a cabo esta actualización con éxito.